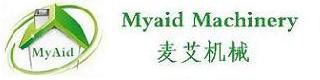
News
how to make good quality eps panels
Eps panels take the largest percentage of the structual insulated panels in the market,so the quality of eps panels is key to the building insulation.We introdue the key below aspects in making good quality eps panels with our 35 years' experience.
1...Good machinery with good panels.
Why you need batch foam machine rarther than continous foam machine.
The advanced batch foaming machine can guarantee the bead density difference in the range of +- 2% after foams. If the bead desity beyond this range,heavier beads will go to the bottom and lighter beads will go up after they go into the aging silos,the finished panels will be different density,even different density for different part of one panel.
And except heavy density panels,batch foam machine can also make light density panels.
Why you need vaccum type styrofoam molding machine instead of air cooling eps forming machine?
Its design can make heating process well-distributed,full beads expansion,little space among beads,low moisture for beads,sound panel shape,it full meets the requirement of the exterior wall panels.Whileas,the low quality molding machine can not control the density of panels,different density for different part of one panel,bog space among beads,not strongly combines,big moisture.
And The vaccum molding machine take 7-8 mins to make one panel,without vacum barrel,it takes 15 mins for one panel.
2... Good quality and well distributed chemicals and chemical prescription.
Panels will be better quality with well distributed beads.You need eps chemicals with bead diameter between 26-28 mesh or 28-30 mesh.Do not mix the diferent bead diameters,this is to gurrantee the eqeal density of panels.If eps chemcal beads are over large,more mositure will be there and more space among beads.If eps chemical beads are over small,the steam will not easily penetrate when heating,so,beads after foams will not bond strongly. The bead size with middle diameter will be the best.
3...Workshop,drying room and warehouse meet the requirement.
Proffesional eps panels factory needs drying room over than 200 ㎡,warehouse over 2000 ㎡.The molding panels will shrink,fastly at begining,then,gradually shrinks.The experiment shows that molding panels need to be placed in natural air for over 42 days,or,over 5 days in 60'C drying room to keep 99.9% stable size.
4...Testing device
Tensile machine,e-balance device,Oxygen testing device guarantee the work.
5...Technician excellence.
Only good technician can make good quality eps panels.Send all technicians to good es panels factory to study.
The reasons for bad quality eps panels....
1.Out of date machines.Panels produced with continious foam machine and hand molding machine are with different density,week bonding and easily break off.
2.Eps chemical problem.cheap materials are over large and over small size,they perform with bad water absorbtion and bonding.
3.Limited aging time
Some small factories have small drying room and warehouse,they supply panels which has not enough time for aging process,if these panels are used on wall insulation,they will be shrinked on wall.
4.Lack of testing device.
5.Quality control problem.Some factories maxmize their profit,they lower density and expand capacity,they even supply 10kg/m3 panels for exterir wall insulation.
1...Good machinery with good panels.
Why you need batch foam machine rarther than continous foam machine.
The advanced batch foaming machine can guarantee the bead density difference in the range of +- 2% after foams. If the bead desity beyond this range,heavier beads will go to the bottom and lighter beads will go up after they go into the aging silos,the finished panels will be different density,even different density for different part of one panel.
And except heavy density panels,batch foam machine can also make light density panels.
Why you need vaccum type styrofoam molding machine instead of air cooling eps forming machine?
Its design can make heating process well-distributed,full beads expansion,little space among beads,low moisture for beads,sound panel shape,it full meets the requirement of the exterior wall panels.Whileas,the low quality molding machine can not control the density of panels,different density for different part of one panel,bog space among beads,not strongly combines,big moisture.
And The vaccum molding machine take 7-8 mins to make one panel,without vacum barrel,it takes 15 mins for one panel.
2... Good quality and well distributed chemicals and chemical prescription.
Panels will be better quality with well distributed beads.You need eps chemicals with bead diameter between 26-28 mesh or 28-30 mesh.Do not mix the diferent bead diameters,this is to gurrantee the eqeal density of panels.If eps chemcal beads are over large,more mositure will be there and more space among beads.If eps chemical beads are over small,the steam will not easily penetrate when heating,so,beads after foams will not bond strongly. The bead size with middle diameter will be the best.
3...Workshop,drying room and warehouse meet the requirement.
Proffesional eps panels factory needs drying room over than 200 ㎡,warehouse over 2000 ㎡.The molding panels will shrink,fastly at begining,then,gradually shrinks.The experiment shows that molding panels need to be placed in natural air for over 42 days,or,over 5 days in 60'C drying room to keep 99.9% stable size.
4...Testing device
Tensile machine,e-balance device,Oxygen testing device guarantee the work.
5...Technician excellence.
Only good technician can make good quality eps panels.Send all technicians to good es panels factory to study.
The reasons for bad quality eps panels....
1.Out of date machines.Panels produced with continious foam machine and hand molding machine are with different density,week bonding and easily break off.
2.Eps chemical problem.cheap materials are over large and over small size,they perform with bad water absorbtion and bonding.
3.Limited aging time
Some small factories have small drying room and warehouse,they supply panels which has not enough time for aging process,if these panels are used on wall insulation,they will be shrinked on wall.
4.Lack of testing device.
5.Quality control problem.Some factories maxmize their profit,they lower density and expand capacity,they even supply 10kg/m3 panels for exterir wall insulation.
Articles from www.insulatedpanelsmachinery.com ,pls mark it with our website if you want to forward the articles
Product Category
Hot Items
Foam Dedusting Crusher - EPS De dust machine
New EPS Styrofoam Densifier Melts without Pre-heating Time
EPS pelletizing machine - strand die works without filtering screen
CNC hot wire 2D cutting machine with wire oscillation
hot wire CNC foam cutting machine with turntable for 2D/3D/4D models
full automatic and continuous eps cutting line
Live Help
0086 13833131292
0086 311 86558425