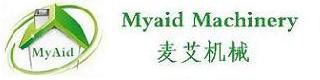
News
DIY hot wire CNC foam cutter
A Hot wire CNC foam cutter is an good tool to have when you make aeroplanes of foam.The hot wire CNC 3D foam cutter allows the ability to cut out any aerofoil shape from a CAD design accurately. A properly configured hot wire CNC foam cutter can save you a lot of effort and produce a smooth finish.This article will give you the workflow on how to DIY make a simple hot wire cnc foam cutter to cut foam wings for prducing a foam airplane.
The machine will have a Nichrome wire (hot wire )stretched between the two towers. The wire is heated by passing current through it and the towers move relative to each other to define the shape of the cut. The 3D CAD design to be cut out is turned into G-code and fed to the machine, which moves in four independent axes to create complex contours like tapered wings.
The motion of each axis which is independently controlled can be achieved by any means such as linear bearings on smooth rods or by using drawer slides of various sizes. Each axis is driven by a stepper motor through a Leadscrew, a GT2 belt and pulley can also be used depending on the size of the hot wire CNC foam cutter . The cutting forces involved in the cutter machine is minimal and the aluminium structure only needs to be rigid enough to withstand the tension of the wire stretched between the towers.Motor is a must on the cutter,we normally use stepper motor for the cutter.
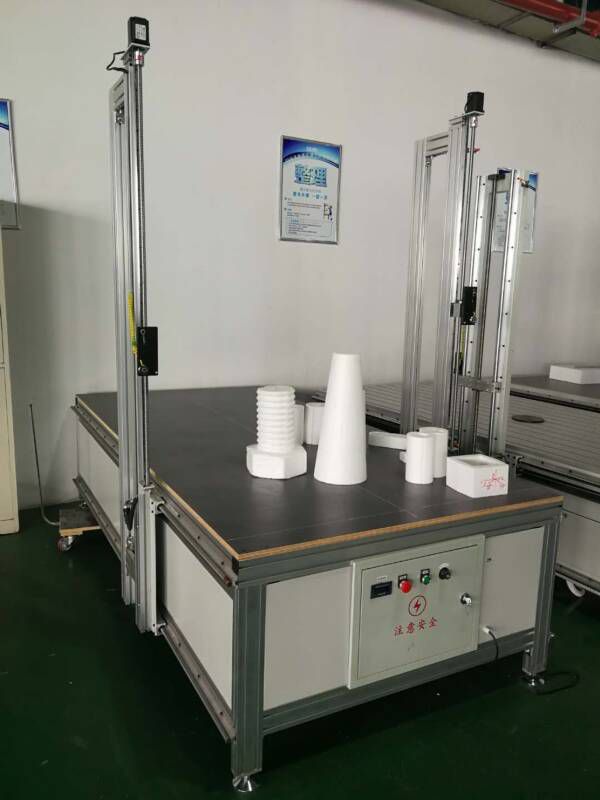
Amazingly,This is a true four axis machine capable of cutting any different shapes on both sides at the same time, before you do next work,the problem will then becomes, how to control 4 independent axes at the same time. Many technician focus on 3 axis machines like 3D printers but there does not seem to be enough documentation on building a four axis machine using easily available parts and open source software. We found a few people who had done similar projects using Arduino and Grbl and decided to make a hot wire CNC foam cutter of our own.
Step 1: Hardware
Depending on the design you like to draw to make you can substitute parts with the ones you find locally at your area,you can also contact us for shipping parts to you,you may spend extra tax if you buy overseas. For example, you can switch the steel tubes/smooth rods with a Drawer slider, which can act as a linear axis.
Plywood (12mm)
Rails (Steel tubes, Smooth rods)
Lead screw (M8 x 600mm, as long as you need the axis to be)
M8-M5 Motor coupler (M8 for the Leadscrew and M5 for the motor shaft)
Arduino Mega 2560
Ramps 1.4 board
Stepper Motors (one on each axis)
A4988 Stepper driver (one for each stepper motor)
12V Power Supply for Arduino+Ramps
Variable power supply (Lipo chargers with Hot-wire mode)
Nichrome wire (32-28 gauge, depending on the size of machine)
The core components and parts are the Arduino Mega, Ramps 1.4, Stepper drivers and motors. The rest of the machine can be made with any design and hardware.
Step 2: Software
Grbl Hotwire Controller
4 Axis G-code Generator
Wing Gcode
Jedicut
FoamXL
The difficult thing in making a 4 axis hot wire CNC foam cutter is finding software to generate the G-code and to drive the machine. There are many people using DevFoam and profilli for generating the G-code and to control their machine. we can supply these controlling software if you buy machine from us.
We make a post,It was for a hot wire CNC foam cutterusing Arduino and GRBL, from there we started building the machine.
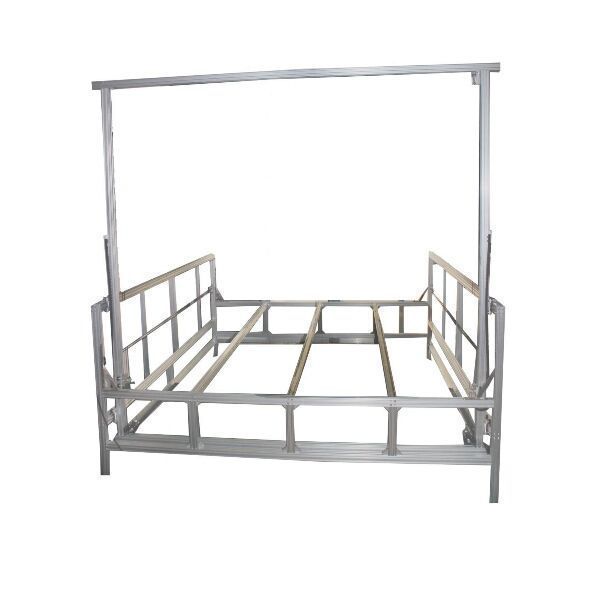
Step 3: Building the Machine
The structure design is made from 12mm plywood, the linear assembly is made using 1/2 inch steel tubes with Plywood sliding blocks.you can also try other options if you like. The design of the sliding blocks is very good,it can be improved to prevent direct contact by introducing a linear bearing or a sleeve. Since we are using Leadscrews, it has enough torque to overcome the friction and still provide good resolution. The two steel tubes give the force of support and constrain the guide block on one axis.
The vertical tower is placed on top of the horizontal guide block, It has four tubes to properly constrain the motion. A minimum of three is required to prevent bending of the vertical tower.this is for the strong structure to make the motion to be stable.
The leadscrew which guide the motion is attached to the stepper motor using the flexible coupling. This helps with any slight miss-alignment between the shaft and the screw. The vertical tower has a stepper motor with an integrated leadscrew, this can be purchased or replaced with an ordinary stepper motor and coupling.
The two towers are mirrors of each other and space is provided in the base to clamp the machine,we will develop new hot wire CNC foam cutter,the space of two towers will be split and flexible,you can adjust the hot wire length,cause it is split body for cutter.
Note- When using sliding surfaces, depending on the material, a phenomenon called 'stick and slip' can happen. This would cause the motion to become jagged and cause vibrations. It may also lead to surfaces locking up leading to excessive loads and missed steps when using a stepper motor.
Step 4: Connecting the Electronics
The next step is to connect the electronics, move the motors, and configure the machine. it is not difficult.We have 4 stepper motors which need to be connected to our Ramps board. The wires need to extend to provide enough travel of the axes.
The wiring on the machine connnect to our Ramps board, which is a CNC shield for Arduino Mega2560. The Ramps can support up to 5 stepper motor drivers like the A4988. We are using Nema 17 motors with 200 steps per revolution running at 1/16th micro-stepping, giving us a smooth rotary motion.
It is important that the A4988 stepper drivers can be attached on top of the Ramps, one for each axis on the machine.And ensure proper orientation of the A4988 chip before attaching to the Ramps board. Each stepper can pull as much as 2 Amps, the stepper drivers have heat sinks to dissipate the heat. The board also has an 11A MOSFET on it to control the temperature of the wire connected to the D8 pin. All the components in the board will get hot, ensure proper cooling is provided.
Important that when the system is powered on, the stepper motors continue to draw current to maintain the holding position.it means the machine is on good condition when it holds the position. The components like Stepper drivers and MOSFETs can get very hot during operation. Do not operate the Ramps board without active cooling.
We laser cut a base for our Arduino and Ramps and attached a 12V DC fan to provide active cooling for the board.
Step 5: Configuring the Machine
Every hot wire CNC foam cutter needs to be properly configured before operating work. Since we are using stepper motors in an open loop system (without feedback) we need to know how far the carriage will move with every revolution of the Stepper motor. This depends on the number of steps per revolution of the motor, the pitch of the lead screw and the level of microstepping you are using.
Motor is important for the motion and we use stepper motor as generally known.We are using a stepper motor with 200 steps/rev, driven using an A4988 driver on 1/16th microstepping, driving a leadscrew with 2mm pitch.
The leadscrew I was using was a two-start one hence the value would be half the above ie- '800' If it is a four-start one then the value would be a quarter of the above value.
After flashing the Mega 2560 with the Grbl8c2MegaRamps file, open the serial monitor and type '$$' to access the Grbl settings panel. In order to change any value type the $number=value. Eg- $0=100 ,you need check it,once the machine is configured, ensure that the machine moves the exact amount as shown in the controller.
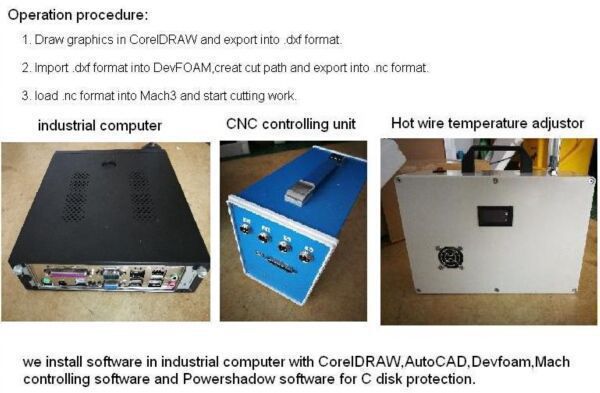
Step 6: Attaching the Hot wire
In order to cut foam, you need a resistance wire(hot wire as generally known) made of a suitable material (nichrome or titanium materials )which can withstand the heat and will have a uniform temperature across its length.
Nichrome is a suitable material, and it is most populiarily used. It is best to have the thinnest wire as possible to decrease the kerf formation while cutting and to give clean cut lines. Generally, the longer the wire, the more tension that must be applied and the thicker the wire must be. So,you need consider the width of your cut,then,design the hot wire length.it may not good if the cutting width is too big.cause it will be not precise in motion.
Experiment with various wire thickness from 32AWG to 28AWG.
The next step for fabricating hot wire cnc foam cutter is to attach the nichrome wire to the machine since we have 4 independent axes, we cannot just tie both ends of the wire to the towers. The wire needs to have some extension to it, either by means of a spring or a weight attached to the end with hanging hammer or a pulley.
Note: Constant tension can be applied to the wire by using a Flat spring (Constant force spring) or by hanging a dead weight at the end. A cheap way to get a constant force spring is by using ID card pull-up reels. Get a good quality one, and you can even stack springs in parallel to provide more pulling force.
Step 7: Control Software and Generating G-code
Grbl Hotwire controller
We are using a Grbl control panel developed by Garret Visser which was adapted for Hotwire cutting by Daniel Rascio. The panel has Independent jogging control for all axis including homing. There is also a Gcode graph visualization tool, and the ability to save your own macros. The Hotwire temperature can be controlled using M3/M5 to turn ON/OFF and S"xxx" command to set the voltage output, either manually or via scrollbar in the software. The hotwire should be connected to "D8" output and is supplied by the power connected to the "11A" input on Ramps.
Wing G-code Generator
Wing G-code Generator is a program to generate XYUV G-code for hotwire cutting model aeroplane wings. It runs on python 2.7 and can also integrate with LinuxCNC's Axis interface. There is also an online version. It allows you to enter the parameters of the wing such as root chord, tip chord, Sweep, gantry length and even support washout. It has a database of airfoils in .dat format. New airfoils can be imported in the same way.
This software is easy to use and supports layering wings on the same piece of foam to save material. The outputted G-code can be sent to the CNC foam cutting machine via the Grbl controller.
Jedicut 2.4
Jedicut is a cool piece of software in that it can do both CAD/CAM and also act as a machine controller. Thought the machine controller needs a PC with the old parallel port interface. It also has a plugin to generate the G-code. It is not the easiest to configure. Some of the options and error messages are in French, but if you sit with it for some time, you can get it working.
It has lots of features like a cutting wizard to help you do sweep wings and compensate for wire kerf by adding a skin thickness. It can cut more than wing profiles, like lettering and other shapes also.
Note- Wing g-code generates G-codes in Absolute mode which works on Grbl without any issues, but Jedicut generates G-code in incremental mode. We had difficulty when first getting it to work, where the machine would just move back and forth. If this happens, Edit the G-code to remove unnecessary lines in the header.
Both Wing G-code and Jedicut generate G-code with some Grbl unsupported codes in the header, The controller will show in the monitor when such errors happen. Edit the G-code and remove unnecessary lines of code.
Working G-codes with both software are included, use them to test out the controller.
Step 8: Setting the Feed Rate and Temperature
The hot wire work on cuts by melting the plastic surrounding it, and when the wire stays in one position for some time, the surrounding foam materials keep melting away. This increases the kerf of the cut and may cause dimensional inaccuracy. we have solutions for it.There are two variables which affect the kerf of the cut.
1. Cutting speed.
2. The temperature of the wire.
The Cutting speed is at which the wire cuts through the material. mostly denotes in mm per min. The faster the speed the smaller the kerf, but the higher the temperature required and also the tension in the wire has to be sufficient to withstand the cutting forces. Good cutting speeds are around the value of 350mm/min to 500mm/min.
One thing need to know that the Temperature of the wire must be a bit higher than the melting point of the foam you are cutting. Ideally, you want to cut with just the radiant heat, when the wire does not actually touch the material but cuts in front of it. The temperature is governed by the amount of current which flows through the wire, which is determined by the voltage applied.Additional knowledge.If you want to put more hot wires ,the voltage transformer on machine is important for the hot wire qty.The bigger the transformer,the more qty of hot wires.
There are software which allows for PWM control of the wire to heat it just at the right moments to optimize the cutting feed rate. The temperature of the wire is determined by the square of the current times the resistance.
If you are using Nichrome wire, Nichrome wire Application Calculator is a cool application that can help you determine the temperature of the wire depending on the length and the voltage applied. For our setup with a wire length of 850mm, we applied a voltage of 26V and cut at a feed rate of 350mm/min.
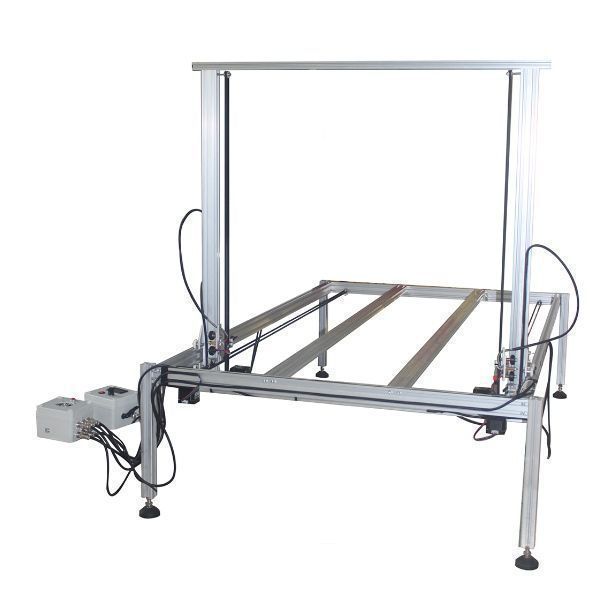
Step 9: Hot wire Cutting Workflow
Take Coreldraw and mach system as example,firstly,you need draw graphics in Coreldraw and export it into DXF format,then,import this DXF format into DEVFOAM,creat cutting path and export into NC format.Lastly,load NC format into MACH system and start cutting work.
The Process starts with the design, which is exported as a DXF. This file is then imported into the CAM software and output as G-code. The machine is turned on and calibrated, the material is placed on the workbench and the origin is now set. Turn on the hot-wire, run the G-code file and watch the machine do the work for you.
I hope you enjoyed the Instructable, do try it for yourself, the machine is easy to build and very forgiving. Many amazing things can be made with it. Happy Flying!
Myaid machinery can supply this hot wire CNC foam cutter by DHL courier.
Product Category
Hot Items
Foam Dedusting Crusher - EPS De dust machine
New EPS Styrofoam Densifier Melts without Pre-heating Time
EPS pelletizing machine - strand die works without filtering screen
CNC hot wire 2D cutting machine with wire oscillation
hot wire CNC foam cutting machine with turntable for 2D/3D/4D models
full automatic and continuous eps cutting line
Live Help
0086 13833131292
0086 311 86558425